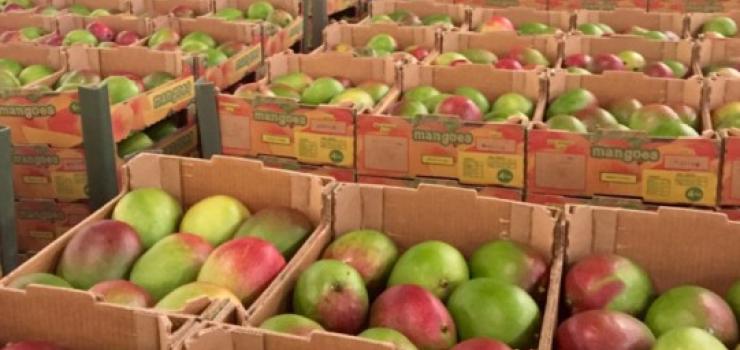
IoT4AGRI Consortium 14 June 2021
Can we overcome this challenge in practice?
This is also the case with mangoes from Van Oers United, being produced in Senegal and transported both via road and sea (Rotterdam) to Dinteloord. When the shipments arrive in Dinteloord, the product loss is being determined. Suppose we could monitor the ripening stage and intervene in the transport chain if needed, we could avoid waste and maintain high-quality products. But is this possible against acceptable cost? To investigate this, we started the IoT4AGRI project.
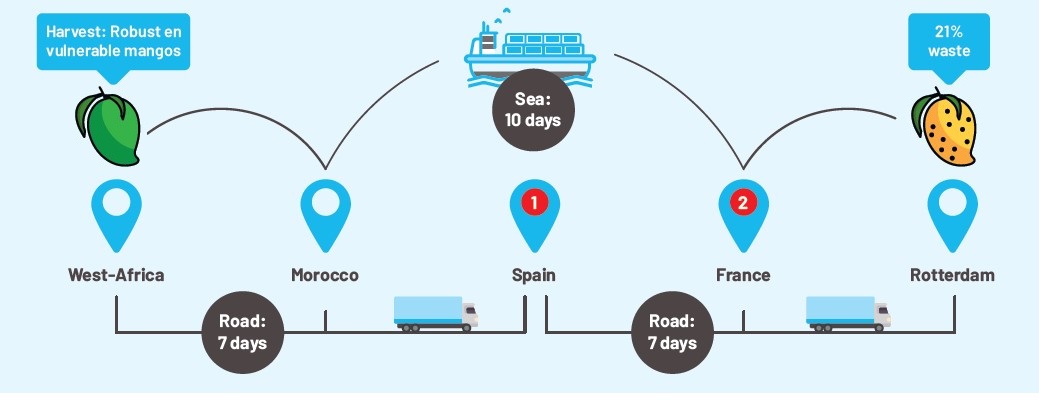
IoT4AGRI integrates sensoring, quality loss modelling and logistics intervention in real-time
In three consecutive steps, we can intervene and avoid waste and quality loss.
- First, we need to monitor and predict the product quality loss. Temperature and humidity variations are important and low-cost sensor solutions already exist. But mangoes and many other climacteric fruits produce ethylene during ripening and this gas accelerates the ripening process. Today, we lack for instance small, affordable and reliable ethylene sensors for transport monitoring, but sensor technology developments are promising.
- Second, there is the challenge of how to get the right sensor data in real-time available for quality loss modelling, also when stuffed in a container and sailing on the open sea. Here, novel cloud communication technologies such as NB-IoT and LoRa offer promising perspectives for low-cost solutions.
- Third, if we have good real-time predictions of the quality loss, can we intervene in the transport chain, and in what way? Can we adjust the conditions in the truck or container, for instance lower the temperature or add ozone? Or can we speed up the transit by deploying a second driver? Can we better reroute the truck and sell the products in Spain instead of receiving rotten fruit in Dinteloord (red dot 1)? Or is unloading the container in Le Havre instead of Rotterdam and selling the goods for the Paris market (red dot 2) the better option? This dynamic intervention is a completely new way of working and requires the right decision support models for executing the right intervention.
In this innovation project, we integrate these three process steps: sensing, real-time quality loss modelling and real-time logistics intervention, supported by a novel cloud data sharing infrastructure solution. And we developed a business case model that shows in what situation and supply chain this concept of integrated quality controlled logistics of perishables is commercially sound, and what the business model looks like.
Do you want to know more?
The project started beginning of 2020. The SmartPort visual gives an overview of the project and its opportunities, challenges and impact. In July 2020 we delivered the first report on the state-of-the-art of underlying technologies and SWOT analysis of the concept. In February 2021 we delivered the second report with the business case findings and the business model considerations. The findings are pretty convincing and reconfirm the commercial attractiveness of the concept. And in April 2021 we delivered the solution development report. Are you triggered or do you think this concept might be interesting for you? Then contact us and explore how your supply chain can be optimized. A fruitful perspective!
This publication is part of the project IoT enabled perishable supply chains (with project number 439.19.609) of the research programme Accelerator 2019 which is (partly) financed by the Dutch Research Council (NWO).
Duration
The project runs from January 2020 until December 2021
More info:
J.K. Boerman
EMS B.V.